Frequently Asked Questions
There’s always question when you’re working or designing with a new material. We’ve organized the most common and useful questions we could think of, to help you learn quickly about Silicone and how Stem Design GmbH can help you get your product made.
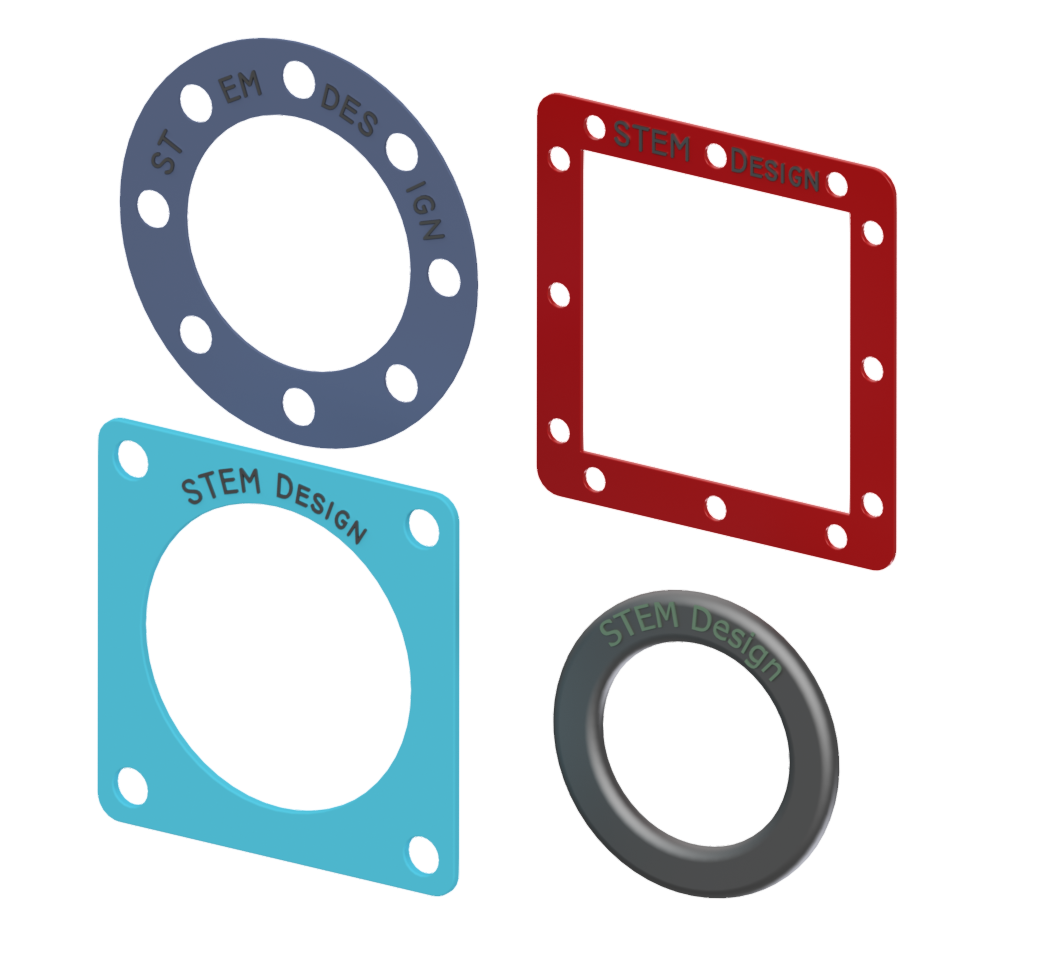
Silicone Parts & Options
Can I just send you a sample and you make it?
Yes! If you have a sample piece of the product you'd like made, that works. Just send us the sample and we'll produce a 3D Model replica of it to get started.
We'll also measure the durometer (hardness) of the piece to make sure you get the same piece.
What file formats do you need to quote? STL? STP?
If you already have an existing design, send us the STP file.
If you only have an STL file, you can send that as well. An STL file only includes the surface, so we will need to confirm the basic dimensions with you to make sure we have the correct sizes.
If you have a sample piece of the product you'd like made, that works also. Just send us the sample and we'll produce a 3D Model replica of it to get started.
What materials are available?
We offer silicone, EPDM, and nitrile rubber.
For silicone, we highly recommend Wacker silicone products. Using a brand name silicone can save a lot of time and paperwork. Wacker is a fellow Munich-based company that offers an incredible selection of silicone rubbers, in nearly any durometer.
For Silicone, we offer 10 Shore A all the way up to 90 Shore A. Our "standard" silicone is Wacker R401, which is available from 20 Shore A up to 90 Shore A. This versatile material can be used for food-grade applications, as well as gaskets and cable guides.
What type of Silicone is available?
We offer 10 Shore A all the way up to 90 Shore A.
Our preference is to use Wacker R401 Silicone Rubber, which is available from 20 up to 90 Shore A. This covers a wide variety of applications, including food-grade parts and industrial gaskets.
Silicone Keypads
How do you design a silicone rubber keypad?
Our Design Guide PDF (Keypad Design Checklist) includes the critical dimensions and rules of thumb to help you design a silicone rubber keypad from scratch.
The key terms to learn are:
1. Key Force : How hard or easy it is to press the button. Measured in grams.
2. Snap Ratio: The "click" you feel when you press the button. A very low Snap Ratio means the user may not be certain if it was pressed properly, but the lifetime of the keypad will be longer. A high ratio and the snap will be very strong, but wear out the part faster.
3. Silicone Web: This is the piece that will flex when the button is pressed. The Web dimensions will change based on the force and snap ratio you select, so don't worry about getting it right! For your design, use a standard .5mm thick web @ 45 degree angle piece. We will have to adjust it to get your force and snap ratio right, and update the model.
4. Contacts: These are typically carbon and are inserted into the mold before the keypad is compressed. The carbon is conductive and will close the circuit on your Printed Circuit board.
5. Backlighting - This is very common in Silicone Keypads today and is done using a slightly different manufacturing process. The silicone material itself is left in its natural color (milky and slightly opaque). The keypad is molded, and then painted black. Your artwork (provided by PDF, JPG or other Photoshop Files) is then laser etched through the black layer. This allows the LED on your PCB to shine through the keypad, and very crisply and clearly display your artwork.
6. Durometer - The durometer is the overall hardness of the keypad. 50 Shore A is very standard for rubber keypads , but we do offer other materials as well.
How is a Silicone Keypad made?
Silicone Keypads are a perfect product for Compression Molding. We use solid silicone and can run them in a wide variety of volumes.
Can you design the silicone keypad as well?
We offer design services for 100 EUR / hour.
A typical part can be completed in 1 -4 hours, depending on size and complexity.
What is your minimum order quantity?
There's no Minimum Order Quantity, but it may be difficult for you to justify the cost a of a custom machined mold for just 1 piece.
Depending on your requirements, we can help with the design and if you only need 1, we can assist with getting the rubber part 3d Printed.
Compression Molding vs Liquid Injection?
Liquid Injection Molding (using a Liquid Silicone Rubber) is a great option for high volume projects (>20.000 pieces).
The majority of our projects are in the 500-5.000 piece range, so we specialize in Compression Molding.
Compression Molding has simpler (less expensive) dies and tooling, so it can save you money compared to the expensive upfront cost of Liquid Injection Molding.
It used to be common that for low durometer projects (>30 Shore A), you were forced to use LSR. This is not true! One more reason for us to use Wacker materials, is they offer 20 Shore A food-grade silicones that are easy to work with, even in Compression Molding.
Orders &
Offers
What type of products do you offer?
Silicone is replacing plastics in a lot of applications, and so it is used in a wide variety of ways.
- Guards and Covers – silicone is used to protest users from heat sources, as well as sharp corners. It can also protect the electronic equipment itself, thanks to how durable it is.
- Electronics – Looking for a case or other way to protect your new device? Silicone is flexible, lightweight and attractive. We can color it or print on it anyway you need to, so it fits your design and aesthetic.
- Custom silicone rubber gaskets – Modern devices are using more and more electronics, PCBs, HMIs and other electronic components. Silicone Rubber is a great way to safe guard these critical components, to ensure a long lifetime between failures.
Can I get my order sooner?
We offer expedited shipping and manufacturing.
Our standard lead time is designed to offer you a low-cost , quality option.
For a first time order ( meaning we need to machine the mold) , delivery is 6-8 weeks.
For future orders, we can usually deliver in 3-4 weeks. These are guidelines, and may vary based on your product design and timing.
Can you design the products as well?
We offer design services for 100 EUR / hour.
A typical part can be completed in 1 -4 hours, depending on size and complexity.
What is your minimum order quantity?
There's no Minimum Order Quantity, but it may be difficult for you to justify the cost a of a custom machined mold for just 1 piece.
Depending on your requirements, we can help with the design and if you only need 1, we can assist with getting the rubber part 3d Printed.
Compression Molding vs Liquid Injection?
Liquid Injection Molding (using a Liquid Silicone Rubber) is a great option for high volume projects (>20.000 pieces).
The majority of our projects are in the 500-5.000 piece range, so we specialize in Compression Molding.
Compression Molding has simpler (less expensive) dies and tooling, so it can save you money compared to the expensive upfront cost of Liquid Injection Molding.
It used to be common that for low durometer projects (>30 Shore A), you were forced to use LSR. This is not true! One more reason for us to use Wacker materials, is they offer 20 Shore A food-grade silicones that are easy to work with, even in Compression Molding.
Stem Design GmbH
E-Mail: sales@stemdesign.de
Telephone: +49 (0) 89/23164900
Privacy Policy
Imprint